汽车 LOGO 作为汽车品牌基因的核心要素,具有强大的吸引力,能够极大程度地聚焦人们的目光。配备精美 LOGO 灯的汽车前脸部分,可显著提升汽车的整体外观质感,吸引更多消费者的关注,助力车辆快速打开市场。 汽车 LOGO 作为品牌商标,在 LOGO 灯开启与关闭的状态下,如何契合车辆整体造型设计要求,成为设计中的关键要点。LOGO 灯作为车辆定位灯系统的一部分,不仅需确保其亮度和外观与其他位置灯协调统一,实现良好的视觉衔接,还必须严格遵循相关行业标准与法规规定。 本文以大众标志为例,详细介绍了 LOGO 灯的内部结构、光路原理以及视觉设计。同时,针对 LOGO 灯中极为重要的外部镜头,提出了三种设计方案,并深入阐述了每个方案的设计流程、优势与不足,旨在帮助读者更全面、深入地了解汽车 LOGO 灯 。 图1. 点亮的汽车LOGO灯 结构与光路
汽车 LOGO 灯主要由六个部分构成,分别是外透镜、内透镜、光学元件、电路板、散热片以及外壳。在组装过程中,第一步是运用螺丝将印刷电路板、散热器、光学元件以及扩散内透镜有序地安装并固定到外壳之上,从而初步搭建起 LOGO 灯的内部结构框架。待内部组件安装完毕后,紧接着进行的是将外透镜焊接至外壳上,以此完成整个 LOGO 灯的组装工作,使其成为一个完整的部件。更为详尽的组装细节与各部件的位置关系,可参照图 2 进行直观了解。
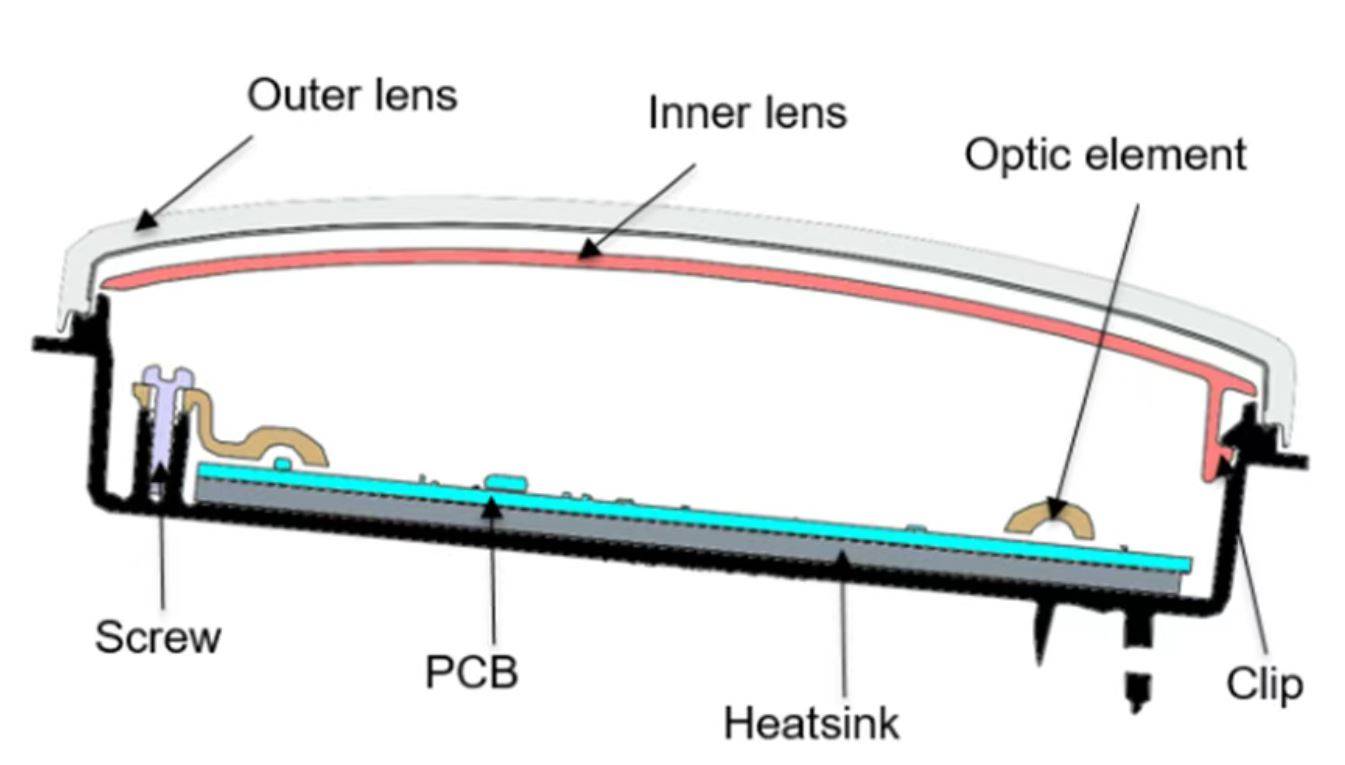
图2. 标志灯的基本结构
由于汽车 LOGO 的外形呈现出环形(如图 3 所示),因此在设计 LED 布局时,也将其设置为环形。这种设计不仅是一种较为出色的光学设计方案,而且从灯具的均匀性设计角度来看,也有着显著的优势。
在 LOGO 灯的工作过程中,光线首先会经过光学元件进行传播,随后透过漫反射内透镜。当 LOGO 灯的尺寸较大时,光线的同质性可能会受到影响而变差。为解决这一问题,通过添加漫反射内透镜,能够促使光线进行再次传播与扩散,从而有效优化光线的同质性,使 LOGO 灯发出的光线更加均匀、柔和,提升整体的视觉效果和照明质量。
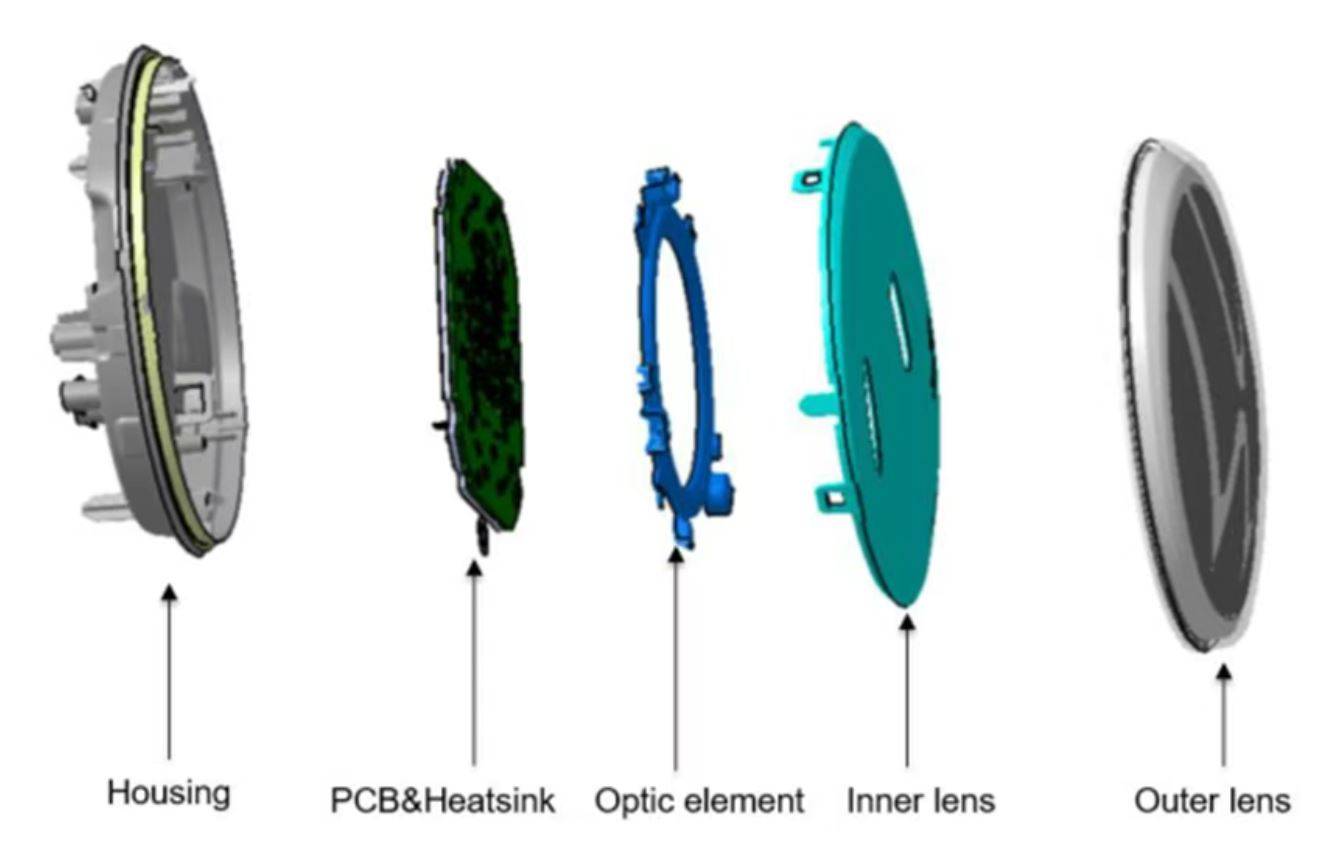
图3. 标志的基本结构
视觉设计
在对汽车 LOGO 灯视觉元素的设计过程中,我们深入研究了两种截然不同的方案,具体情况如图 4 所示。其中一种方案是采用反射器,而另一种方案则是运用准直器。从实际的设计与应用角度来看,这两种方案均具备可行性,然而,它们各自也存在着独特的优点与不足之处。接下来,为您详细介绍这两项方案:
(1)反射器方案
为了有效应对点光源所导致的光分布不均匀这一难题,我们对垂直反射器的方案展开了深入研究。该方案中,垂直反射器能够确保光线在水平方向上进行有效传播,与此同时,扩散器的存在则进一步保证了光线在垂直和水平两个方向上都能实现良好的传播。经过这一系列的光学处理后,光线最终到达最后的外部镜头。综合来看,这一光学方案呈现出以下主要特点:
- 更好的光色控制
:由于反射器和扩散器对光线的传播路径和方向进行了较为精确的控制,因此能够实现对光色的更好把控,使得最终输出的光线颜色更加准确、稳定,符合设计预期和实际使用需求。 - 需要更多的光散布空间
:为了实现光线在水平和垂直方向上的充分扩散,该方案需要相对较大的空间来容纳反射器、扩散器等光学元件,以便为光线的传播和散布提供足够的空间,这在一定程度上可能会对灯具的整体尺寸和结构设计产生影响。 - 存在 LED 热点的风险
:尽管反射器和扩散器在一定程度上能够改善光分布的均匀性,但由于点光源本身的特性以及光学元件的工作原理,在某些情况下,仍有可能出现 LED 热点的情况,即局部区域的光线强度过高,影响整体的视觉效果和照明质量。
(2)准直器方案
在这一方案中,光学准直器发挥着关键作用,它能够有效地帮助 LED 光源传播光线。光线首先穿过漫反射内透镜,经过漫反射内透镜的处理后,光线进一步扩散和均匀化,最后到达外面的镜头。这一光学方案的主要结论如下:
- 更好的折射效果和光色散
:准直器能够对光线进行有效的准直和引导,使得光线在传播过程中能够更好地发生折射和色散现象,从而实现更均匀、更柔和的光线输出,提升视觉效果。 - 节省更多的空间
:相较于反射器方案,准直器方案在空间利用方面具有一定的优势。由于其结构相对简单,不需要像反射器方案那样占用大量的空间来实现光的散布,因此能够节省更多的空间,为灯具的紧凑设计提供了可能。 - 没有 LED 热点的风险
:由于准直器和漫反射内透镜的协同作用,有效地避免了 LED 热点的产生,使得光线在整个输出区域内分布更加均匀,提高了照明的质量和稳定性
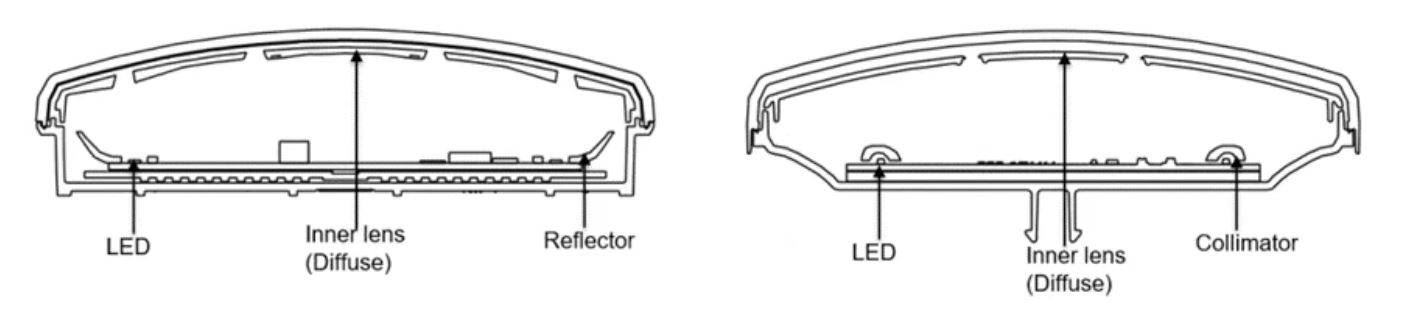
图4. 反射器和准直器方案
外透镜设计
汽车 LOGO 灯设计的核心要点在于外透镜的研发。针对外透镜的工艺,我们深入探讨了三个可行的方案,分别是 IML 方案、3D 打印方案以及 2K 方案。在近期的研究中发现,这三种方案各有优劣,以下是对它们的详细介绍:
(1)IML 方案
IML 方案的制造过程示意图如图 5 所示。首先,使用油墨将商标的黑色部分印刷在平面薄膜上,随后通过真空成型的方式,使薄膜塑形为标志外透镜的形状。接着,把成型后的薄膜放入模具部件中,启动注射成型工序。在这一步骤完成后,还需对外透镜的后表面进行镀铝处理。最后,借助激光工艺生成透明线条,从而在发光面上形成更为清晰的边界。
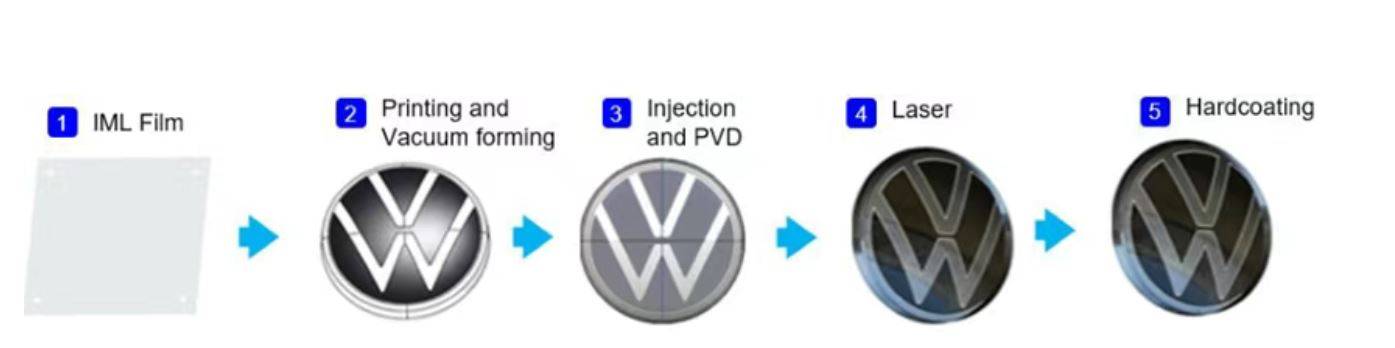
图5. IML方案制造外透镜的过程
(2)3D 打印方案
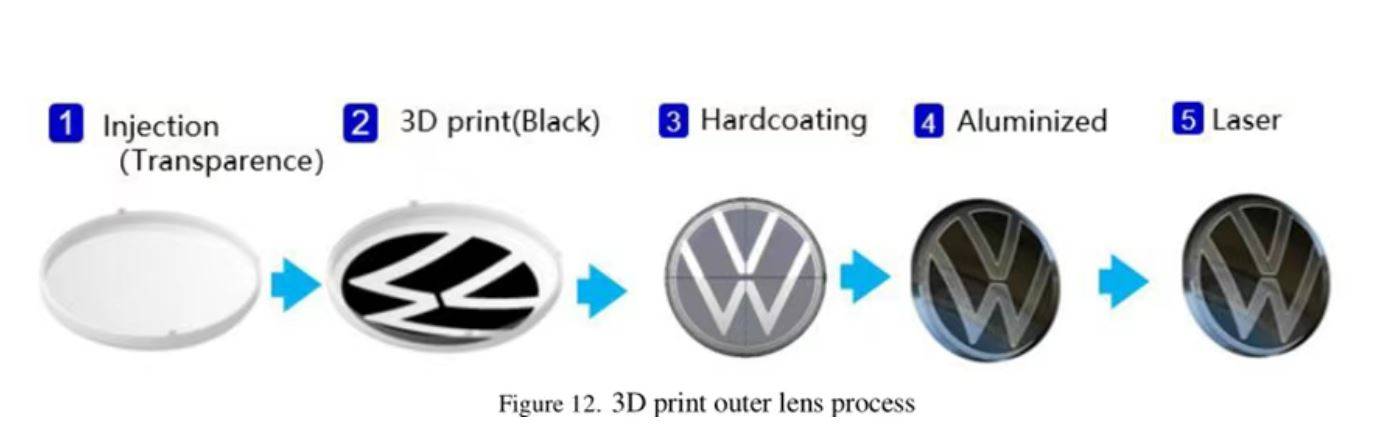
图6. 3D打印外透镜的过程
(3)2K 方案
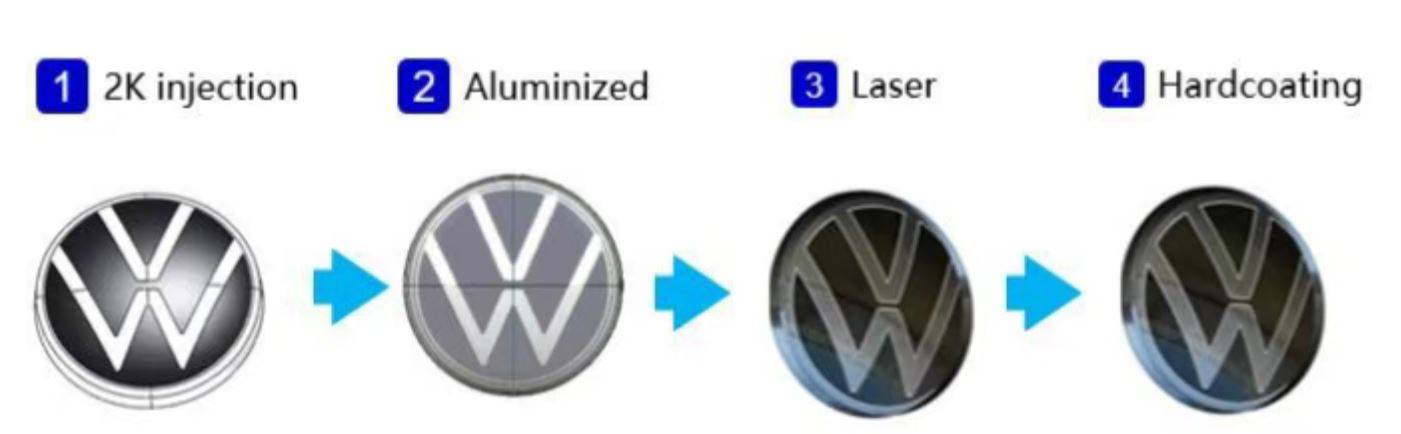
图7 2K方案制造外透镜的过程
结论
本文以大众 LOGO 为例,深入剖析了汽车 LOGO 灯的结构,并围绕其结构、光路以及视觉设计展开探讨。针对 LOGO 灯中至关重要的外部镜头,提出了三种设计方案,分别为 IML 方案、3D 打印方案和 2K 方案,详细介绍了各方案的制作流程以及优缺点。
经对这三个方案的深入研究发现,2K 方案相较于 IML 方案和 3D 打印方案优势显著。尽管采用 2K 方案需要投入更多的模具成本,但其能够打造出高品质的黑边,而且工艺简洁、产品质量率高。3D 打印方案可作为次优选择,该方案虽能节省部分模具成本,但质量率方面存在较大问题。若设计方案对公差的敏感度较低,同时对边缘质量有较高要求,那么 3D 打印方案不失为一种可行的解决途径 。
文章转自 微信公众号 陈同学的车灯设计汇
发表评论 取消回复